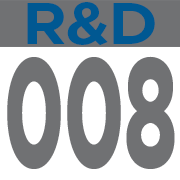
Today we bring you this study on the LSR injection process that has been developed by Sang-Gweon Kim, Hyung-Pil Park, Jeong-Won Lee, Yong-Jun Jeon, Baeg-Soon Cha.
Heat Treatment R & D Group, Research Institute of Advanced Manufacturing Technology, KITECH (Korea Institute of Industrial Technology), Incheon, Korea
This study explores molding processes using the multi-component injection molding (MCM) method. In this method monolithic products are molded in such a way that it is possible to bond mixed liquid silicone rubbers (LSR) to polybutylene terephthalate (PBT). The latter has the characteristic of self-bonding during combustion due to Pt catalysts. It is possible to observe that this method increases the bonding force between LSR and PBT.
Surfaces coated with Polytetrafluoroethylene (PTFE), Cr, Ni, etc. they have excellent peeling with plastic. We can also compare these surfaces with those treated with hot forging die and micro shot blasting without coating.
When peeling tests are performed at the specified polymerization temperature and molding time after LSR molding on these surfaces of hot working die molds without coating, these surfaces show excellent peeling of molds and LSR products. In particular, they show better peeling after micro blasting than surfaces with Cr and Ni coating as well as surfaces without coating, and the peeling strength also decreases.
The results of the contact angle and the XPS analysis indicate that the binding force of the LSR increases as an effect of the catalysts, although by SEM it is not possible to find it. According to XPS analysis, the surface structures are close to the methyl and vinyl materials produced during LSR molding.
Method and findings.
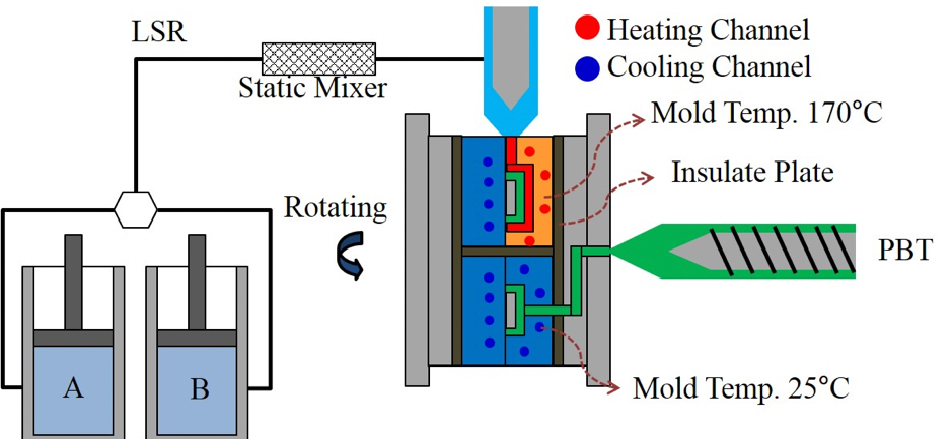
The specimen of the bottom mold was etched for 10 minutes after performing LSR molding once and again after LSR molding repeated 5 times, and the foreign material was removed.
Next, the binding energy was then measured by an XPS device. In other words, these oxide structures are stable in the Si bonds, and the C structures with micro blasting have more C-C/C-H than C-Si. In the cases of PTFE coating, C-Si structures are remarkably dominant than C-C/C-H and should form stable films on surfaces to decrease reactions with LSRs; and peeling is excellent even though the contact angle is less than 120 ̊.
Copies:
- The study discussed peeling problems with molds and products, caused by the material added to enhance the peeling strength.
- Performing a microblasting treatment instead of coating for LSR injection and molding when we overmold PTFE.
- LSRs have been used for insulation of wires and plugs because they are good elastomers excellent in sealing, adhesion, etc.
- Production of high quality products through an LSR injection process.
In most cases, coatings have very complex shapes on the surfaces of complicated molds.
In this link you have the complete text of this study on the LSR injection process