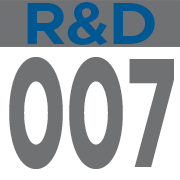
LSR bonding is essential, as different markets use liquid silicone rubber to produce a wide range of parts. On this occasion Mr. Paul A. Wheeler, Mr. Carney, Mr. Douglas H. Mowrey, Ms. Rebecca S. Cowles and Mr. Tarek A. Agag bring us the results of their interesting investigation.
Thus Rubber & Plastics News magazine wrote this very interesting article. Undoubtedly almost all the manufacturers need Silicon bonding to other substrates. In essence a great summary of adhesion in between silicone and thermoplastics and metals.
Reproduction of the Executive Summary
Lord Corp. offers new adhesive solutions that effectively bond platinum-cured liquid silicone rubber to various substrates directly in an injection or compression molding process.
This technology does not require plasma treatment or other complicated and costly surface preparation steps.
In this study, it is possible to bond LSR with several substrates thanks to the test with three new adhesives. These included polycarbonate, thermoplastic elastomer, polyamide, and stainless steel.
Subsequently, there is a process of molding the pieces, to finish with peeling tests. Therefore, this process and product technology offers a number of benefits compared to existing technology. Of note are greater design freedom, more robust processing, fewer surface preparation requirements, and environmental friendliness.
LSR molding
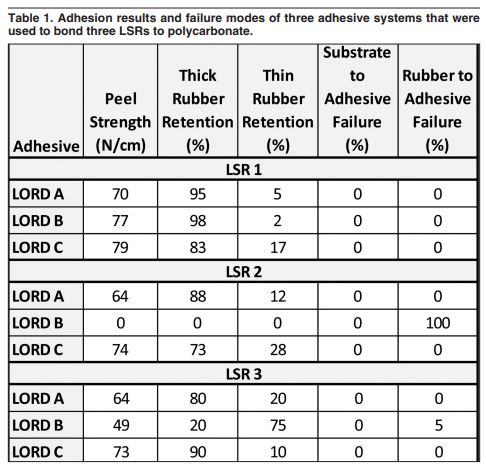
The LSR silicones supply is in two separate reactive components. Before molding it is necessary to mix them. In a Kitchen Aid mixer at low speed and for five minutes, mix both sides of silicone. The substrate was overmolded with LSR in a Wabash MPI G30H-18-BX compression press that was heated to 125°C.
In each cycle, three pieces of substrate were placed into a 150mm x 150mm x 5mm mold, along with 150 rams of LSR.
The parts are then molded by subjecting them to 20 tons of pressure for five minutes. Fig. 1 shows an example of the test pieces used and the mold used to create LSR test specimens.
After five minutes, and allowing the parts to cool to room temperature, they were carefully removed. The LSR is cut into 25mm wide strips to perform the peel test.